The Essential Benefits of Testing and Tagging Electrical Appliances and Equipment
The Essential Benefits of Testing and Tagging Electrical Appliances and Equipment
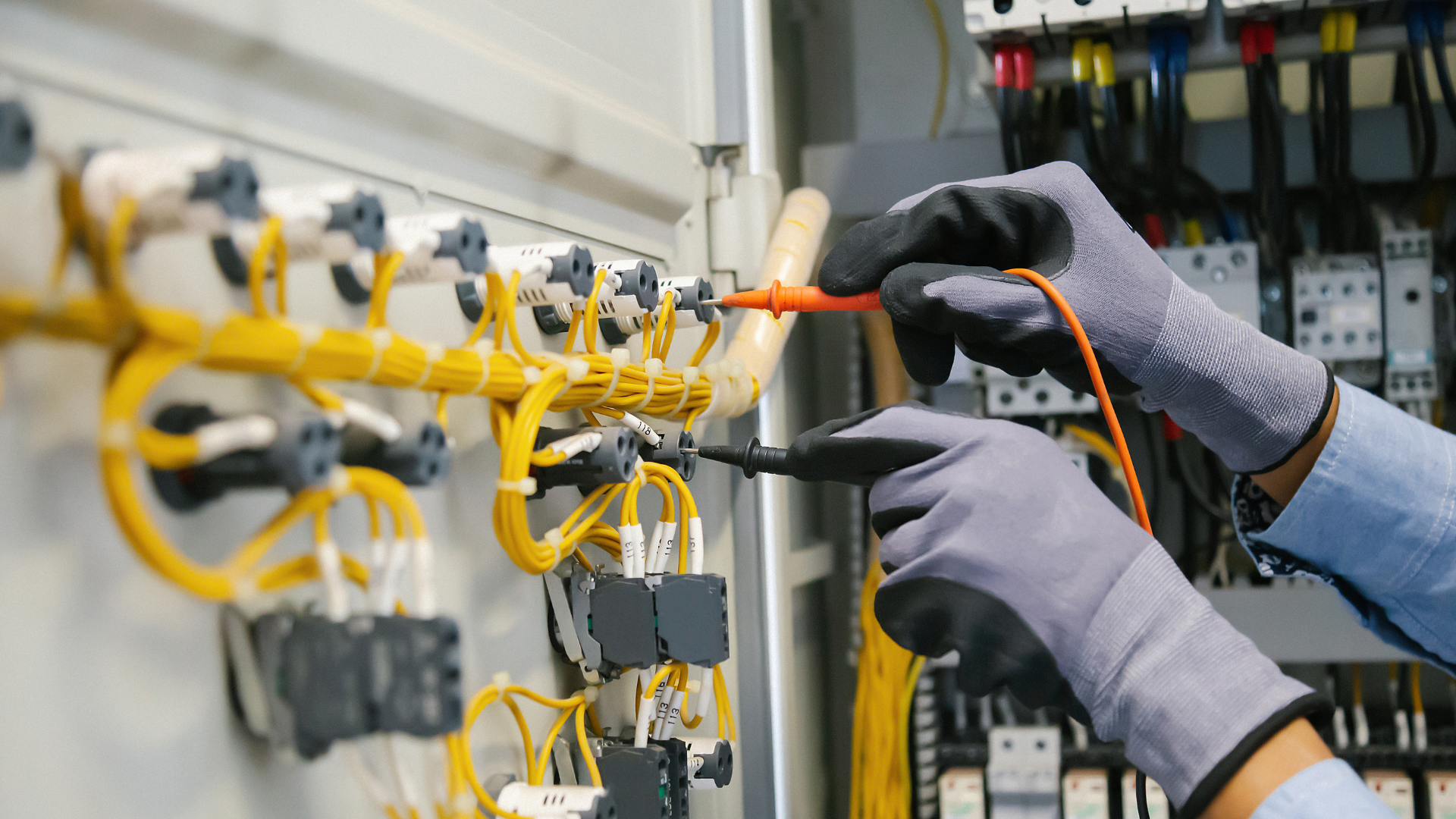
In today’s fast-paced world, businesses rely heavily on electrical appliances and equipment to keep operations running smoothly.
From offices buzzing with computers and printers to bustling construction sites with heavy-duty tools, electricity powers it all. Yet with this reliance comes a significant risk: electrical faults that can lead to accidents, injuries, fires, or even fatalities.
That’s where testing and tagging steps in—a systematic process that ensures electrical appliances and equipment are safe to use. Though it may sound like a compliance formality, testing and tagging provides far-reaching benefits that protect people, property, and productivity.
Let’s explore what testing and tagging is, why it’s so critical, and the key advantages it brings to workplaces of all shapes and sizes.
What is Testing and Tagging?
Testing and tagging involves two crucial steps:
- Inspection and Testing: A qualified technician visually inspects the electrical item for obvious damage (like frayed cords or cracked casings) and then uses specialized equipment to test for internal faults, insulation resistance, and earth continuity.
- Tagging: After passing the tests, the item is fitted with a durable tag indicating it has been tested, the date it was tested, the next due date for testing, and who performed the work.
This process is guided by Australian standards such as AS/NZS 3760, which set out the recommended procedures and testing intervals for different types of environments.
The Essential Benefits of Testing and Tagging
1. Enhances Workplace Safety
Above all, testing and tagging is about keeping people safe. Faulty electrical equipment can cause electric shocks, burns, or fires. Regular inspections and tests detect problems early—before they can harm employees, contractors, customers, or visitors.
For example, a power tool with a hidden earth fault might still function normally, but it poses a serious risk of electric shock. Through testing, this defect is uncovered and can be fixed or the equipment removed from service.
In industries like construction, manufacturing, hospitality, or healthcare—where the use of portable electrical equipment is high—the importance of these checks can’t be overstated. They help create a safe environment where staff can focus on their work without fear of unseen electrical hazards.
2. Reduces the Risk of Electrical Fires
Electrical faults are among the leading causes of workplace fires. Damaged wiring, loose connections, or failing insulation can overheat and ignite surrounding materials.
By systematically testing appliances, cables, extension leads, and power tools, you drastically reduce the likelihood of an electrical fault developing into a fire. This proactive approach protects not only your employees but also your premises, valuable equipment, and critical data.
Preventing even a single electrical fire can save tens or hundreds of thousands of dollars in damage and operational disruption.
3. Ensures Legal Compliance and Protects Your Business
Under Australian workplace health and safety laws, employers have a duty to provide a safe working environment. In many industries and jurisdictions, regular testing and tagging of electrical equipment isn’t just a recommendation—it’s a requirement.
Failing to comply with these obligations can lead to:
- Fines and penalties: Regulators take safety breaches seriously, and penalties can be substantial.
- Increased liability: If an incident occurs and it’s found that the business neglected to test and tag equipment, the consequences could include lawsuits or insurance claims being denied.
- Reputational damage: News of a workplace incident caused by preventable negligence can harm customer trust and staff morale.
By maintaining a robust testing and tagging program, you demonstrate due diligence and ensure you’re meeting your obligations under WHS laws.
4. Prolongs the Life of Equipment
Regular testing doesn’t just identify dangerous faults; it also helps detect wear and tear that, if left unaddressed, could cause premature equipment failure.
For instance, discovering a minor issue—like a loose internal connection or degraded insulation—allows you to repair or replace the component before it fails completely. This means your investment in electrical equipment goes further, reducing costs over time.
Businesses often spend substantial amounts on their tools, computers, machinery, and appliances. Testing and tagging helps protect that investment, extending the lifespan of your assets.
5. Minimizes Downtime and Keeps Operations Running
Imagine the cost of a critical tool suddenly failing on a busy construction site, or a faulty server room cable taking down your entire office network. The disruption could mean missed deadlines, unhappy customers, and lost revenue.
Through routine inspections, testing and tagging highlights potential issues before they escalate into disruptive breakdowns. Faulty items are either repaired or safely removed from service, keeping your operations running smoothly and reducing the risk of sudden, costly interruptions.
6. Builds a Strong Safety Culture
When employees see that you take testing and tagging seriously, it sends a clear message: their safety matters. This promotes a broader culture of care, responsibility, and attention to hazards.
Staff are more likely to report concerns, use equipment properly, and stay vigilant. Over time, this kind of proactive safety culture can reduce accidents and improve overall morale and productivity.
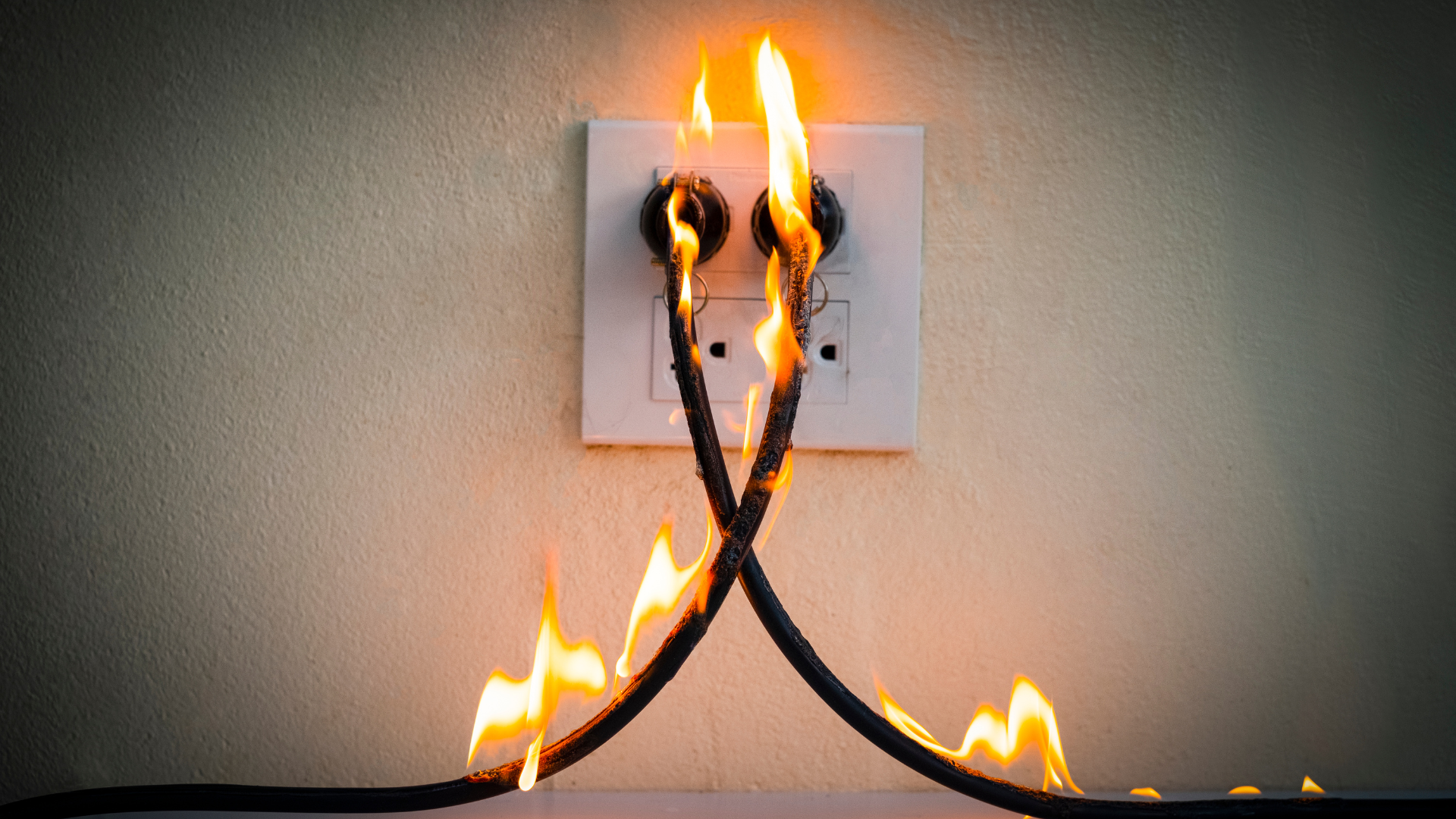
7. Supports Accurate Record-Keeping and Auditing
Testing and tagging generates a clear paper trail (or digital record) of compliance. This can be invaluable if you’re ever audited by a safety inspector, insurance assessor, or legal investigator.
Detailed logs show exactly what was tested, when it was tested, and by whom. They provide proof that you’ve met your obligations and taken reasonable steps to maintain a safe workplace.
These records also help you keep track of equipment lifecycles, plan for replacements, and schedule future testing—taking the guesswork out of safety management.
8. Boosts Client and Customer Confidence
In some industries, clients expect proof that your business takes safety seriously. Testing and tagging certification can give your customers confidence that your equipment is safe and that you’re a professional, responsible operator.
This can be especially important for contractors bidding on projects—many commercial contracts now require up-to-date test and tag documentation before work even begins.
How Often Should You Test and Tag?
Testing frequency depends on several factors, including:
- The type of environment (e.g., construction sites require more frequent testing than low-risk offices).
- The nature of the equipment (portable and flexible cables generally need more regular checks).
- Manufacturer recommendations and Australian Standard AS/NZS 3760 guidelines.
For example:
- On construction and demolition sites, equipment is typically tested every 3 months.
- In factories or workshops, intervals might be 6–12 months.
- In offices, where the risk is lower, testing might be required every 1–5 years.
It’s essential to consult a qualified testing and tagging professional who can assess your specific needs.
Final Thoughts: A Small Cost for Significant Peace of Mind
Ultimately, testing and tagging electrical appliances is a modest investment that delivers substantial returns. It safeguards your employees, protects your property, keeps your business compliant, and can even save you thousands by preventing fires or breakdowns.
Most importantly, it provides peace of mind—knowing that you’ve taken proactive steps to identify and eliminate hidden electrical hazards.
If your business relies on electrical equipment—and virtually all do—don’t wait for a shock, spark, or insurance claim to highlight the importance of safety. Schedule regular testing and tagging with a qualified provider and enjoy the confidence that comes from knowing your workplace is secure.
Ready to protect your workplace?
If you’d like help organising a tailored testing and tagging program for your business, or want to learn more about your obligations, reach out to a trusted local electrician or safety specialist.
They can provide advice specific to your industry and ensure you stay compliant and protected.
✅
Quick Takeaway:
Testing and tagging is more than a compliance checkbox. It’s a critical safety strategy that:
- Keeps people safe from shocks and fires
- Reduces liability and meets legal obligations
- Extends the life of valuable equipment
- Minimises downtime and costly disruptions
- Promotes a culture of safety in your business
Stay proactive—because when it comes to electricity, prevention truly is the best protection.
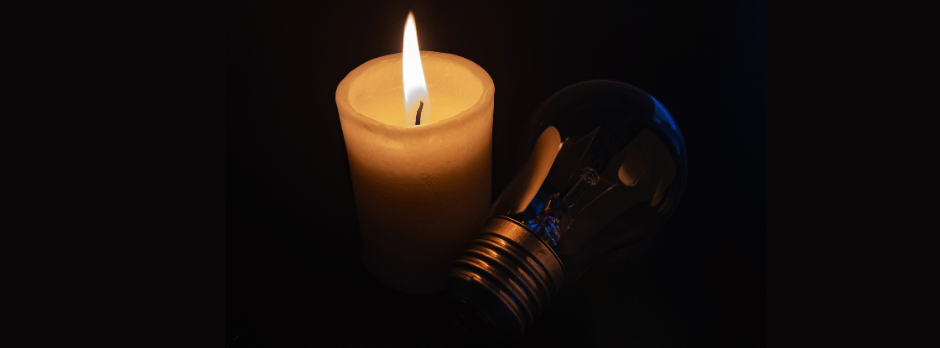
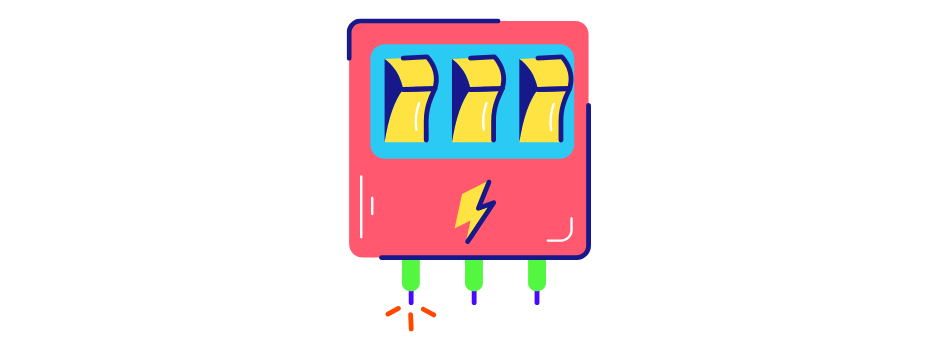
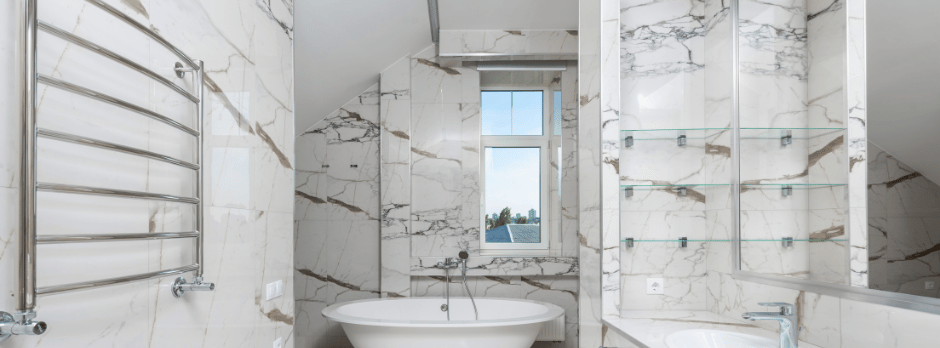
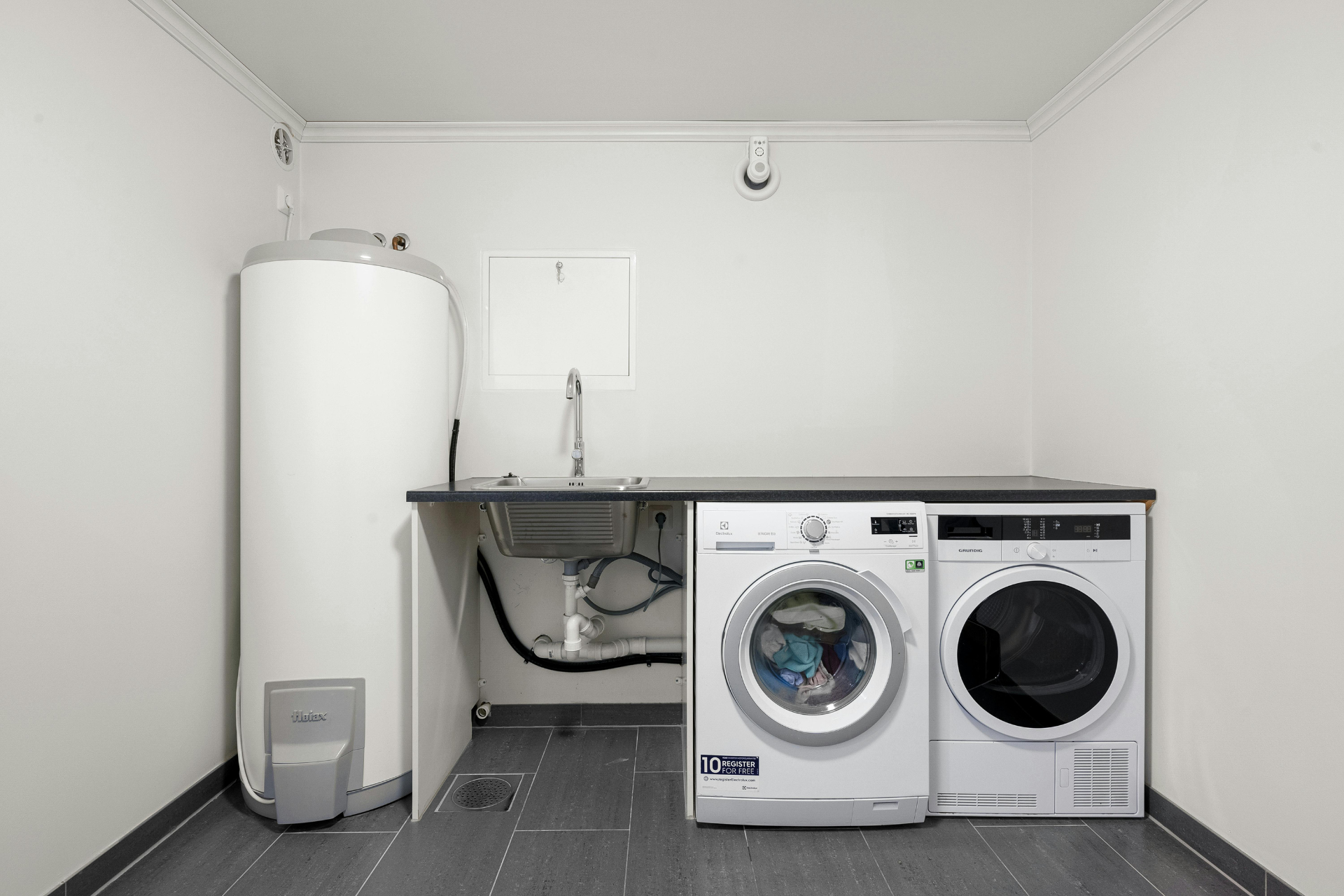
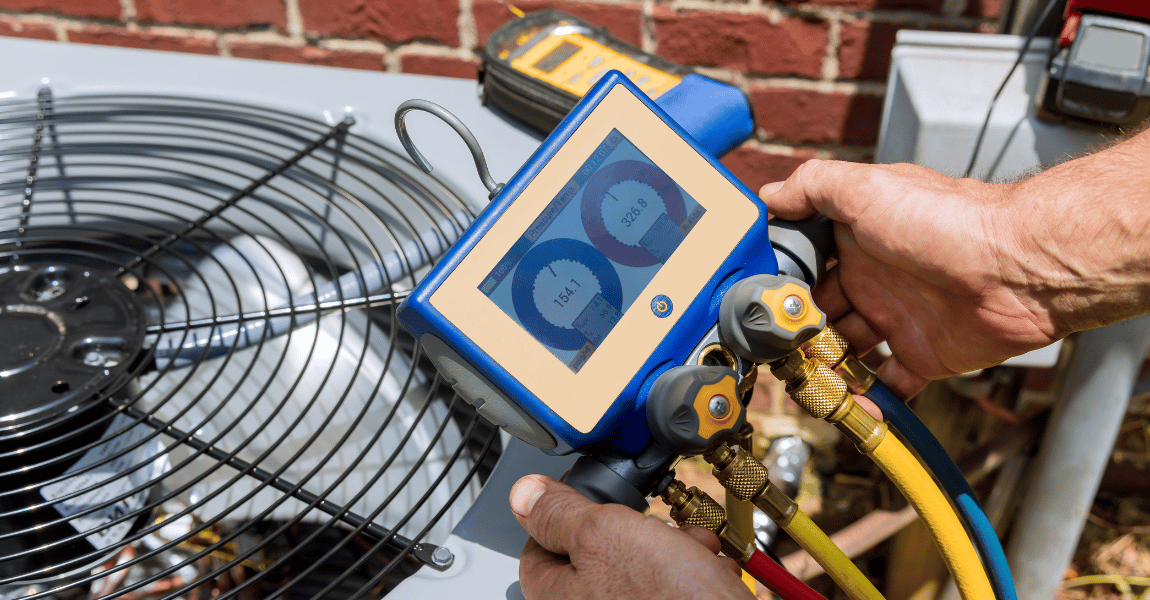
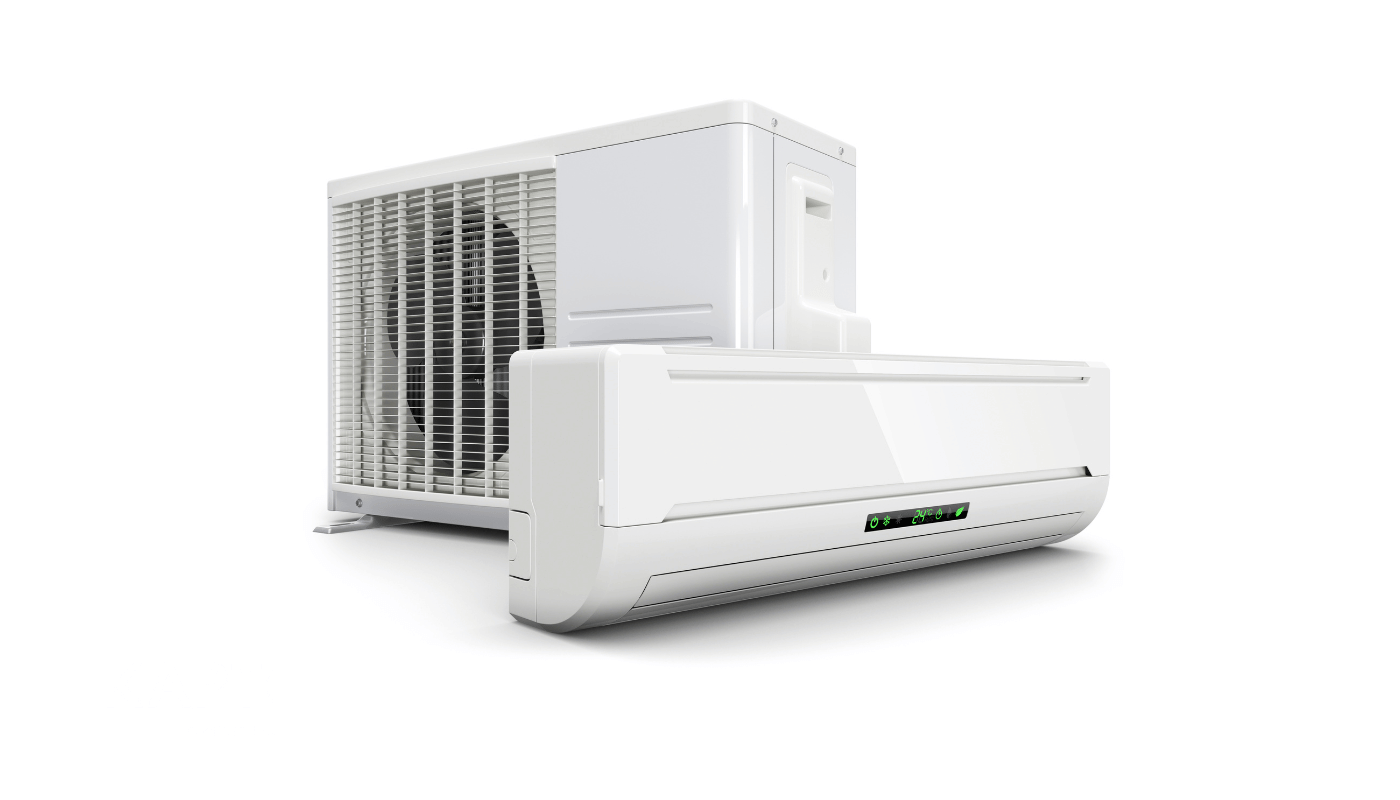
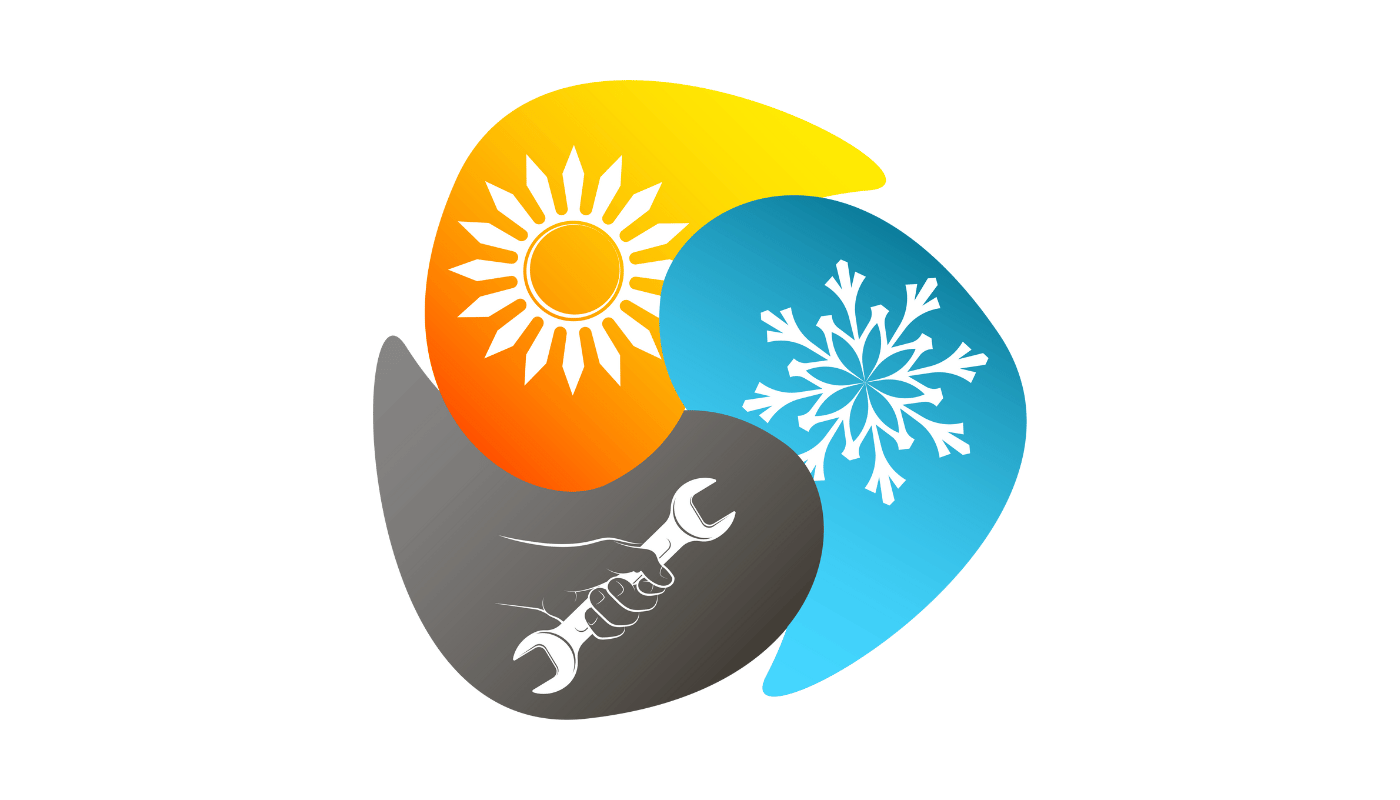